Our robot
FIRST DEEP SPACE: Banshee
The season of 2019 presented a variety of problems for us to solve in unique and innovative ways. We were required to intake and deposit a disc with velcro edges, and a large, soft ball which needed to be deposited at a number of different heights. This resulted in a complex, and robust robot which was designed with a strategy in mind.
Our first step was to remove tasks which were not worth pursuing: the best approach was to do a few tasks efficiently and reliably, than do everything poorly. The tasks that we chose to pursue were hatches (velcro discs) and cargo (rubber balls) on the lowest level with the idea that we could quickly shuttle game pieces and maintain stability. We opted to intake cargo from the ground but found little downside in intaking hatches from the intake stations at the end of the field. The strategy we had devised required agility and speed, so the decision to use our custom-built swerve drive was unanimous. We also decided that climbing to the highest level was a worthwhile endgame strategy, enabling us to maximize our potential score in the last 30 seconds of game time. With this in mind we set out designing our robot
Auto Mode
Advanced Autonomous Mode
Our autonomous routine took advantage of the hatch mechanisms flexibility and robustness. While this season presented the opportunity to have drivers control their robots using cameras and other sensors during the first 15 seconds, the Drop Bears chose to have the robot autonomously manoeuvre itself and deposit two hatches. We would score the first hatch panel reliably, but the second hatch proved difficult with time constraints. The routine itself was more efficient than many manned robots particularly for the auto climb routine, and won us awards for the unique approach, and the elegance with which it was able to perform the routine.
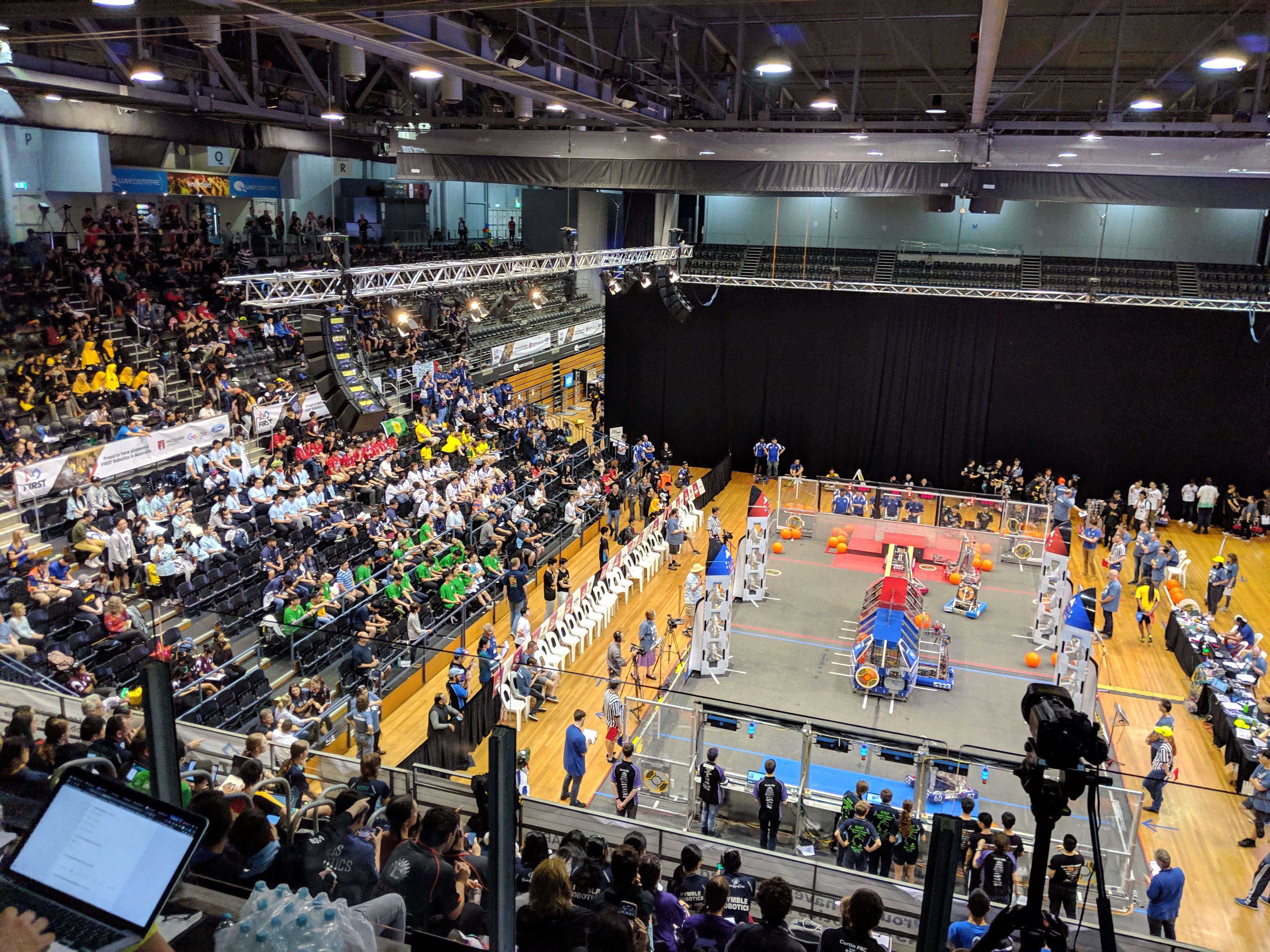
Hatch Mechanism
Our hatch mechanism was designed to take advantage of the velcro around the edges of the hatch panel. The idea was to develop a simple, static mechanism which was tolerant to misalignment, allowing the driver to focus on the matter at hand. The mechanism went through a couple of revisions upon discovering that the velcro used rapidly deteriorates, which led to us using a more active mechanism featuring pistons to attach to the inside hole of the hatch. This resulted in an effective, and durable method of manipulating hatches.
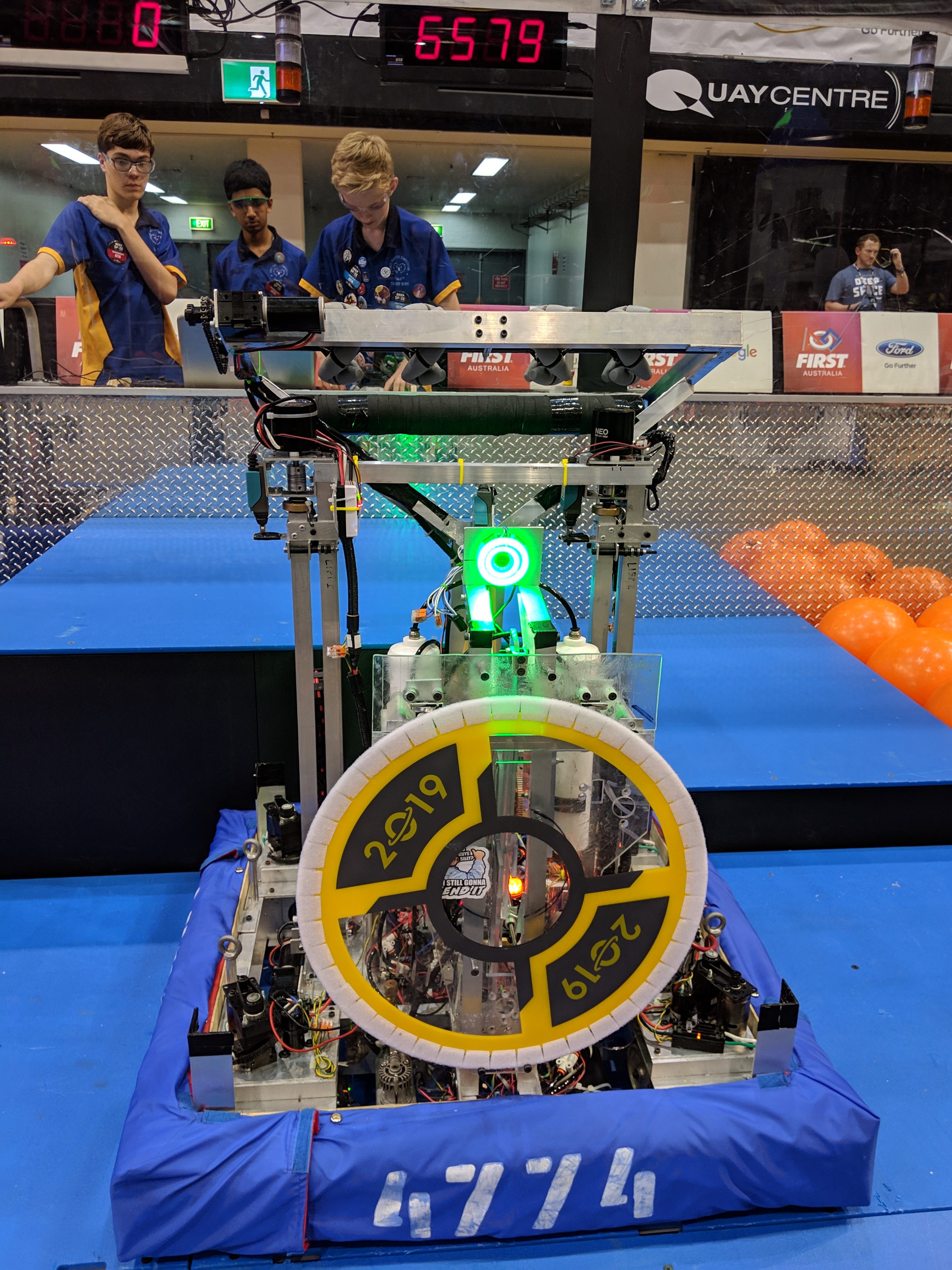
Cargo Mechanism
Our cargo mechanism needed to be able to intake from the ground and deposit to the cargo ship. This meant our mechanism needed to operate at two different heights. The easiest way of doing this was to use a pivoting arm to raise and lower the cargo balls. The arm was powered by a neo motor and was gear driven. To intake the ball itself we used a horizontal roller with mecanum wheels to center the ball. This meant the position of the ball was predictable and the driver could routinely deliver cargo to the cargo ship without having to compensate for misalignment. The cargo mechanism was effective and eventually became our primary source of points, and focus during games.
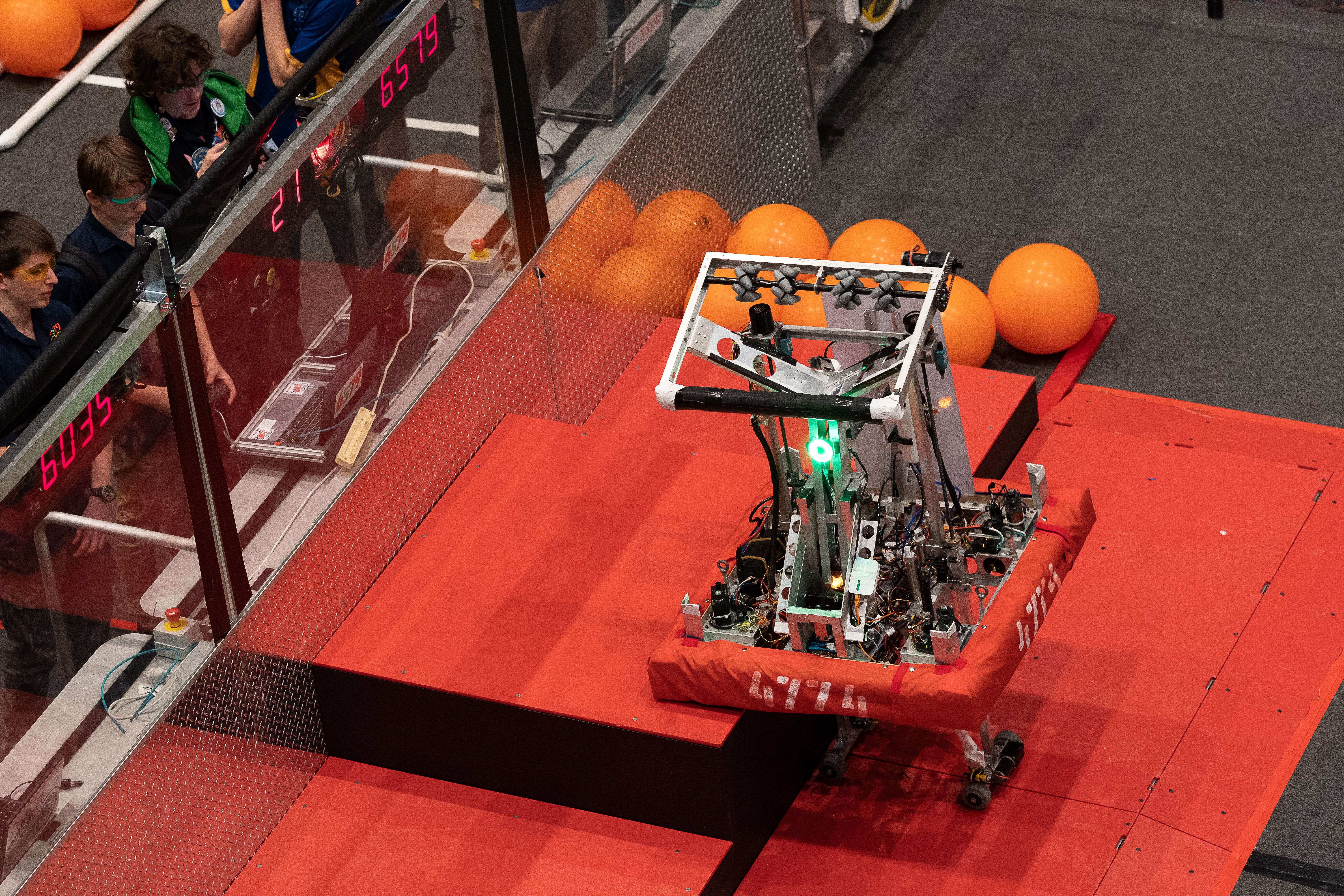
Climbing mechanism
Making the robot climb was one of the most difficult tasks we were presented with. We devised a solution which would lift the robot on two legs, drive it forward, and retract each leg as the robot was supported by the platform. The bumpers would hang below the top of the platform, so the robot would deploy three pneumatic pistons to give it the extra height required. The legs were driven by lead screws and neo motors, making the mechanism fast, and simple. The climbing mechanism was our most reliable with a 100% in game success rate for games where we chose to climb. It was also a rarity at regional events to see a climbing robot, and was a great achievement for the team that we were able to build such a reliable mechanism.
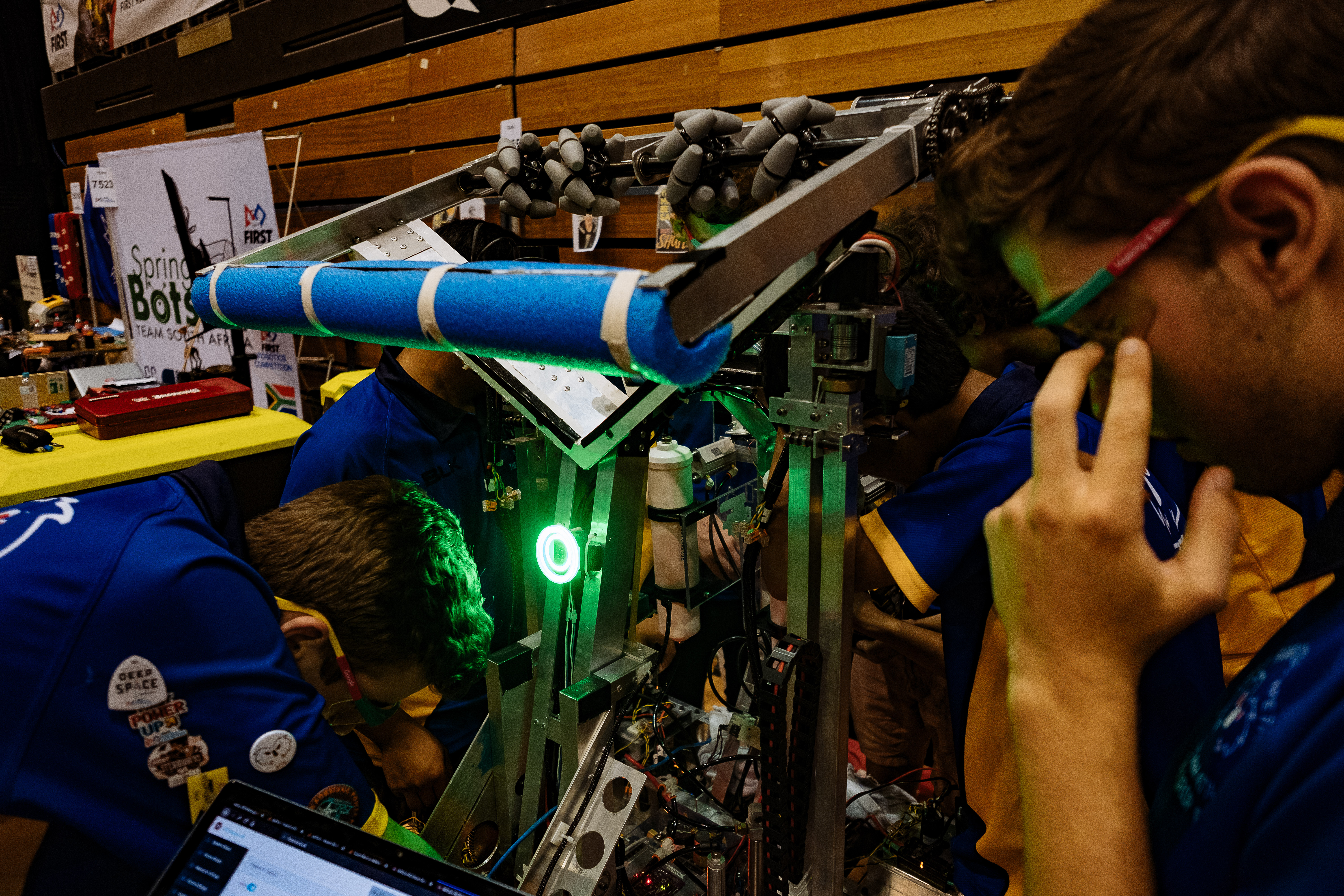
drive base
Swerve Drive
The season of 2019 was the debut of our second generation swerve drives. The module was smaller, faster, easier to maintain, and more capable on the field than the previous model. The heavy miniCIM motors were exchanged for the much smaller 775pro motors, and the steering assembly was also adapted to use the same motor. It was also designed to be easier to work on, with steering gears moved to the top of the module for accessibility. The modules were unique to the Drop Bears, and sparked curiosity and interest at all three regional. The modules allowed us to be incredibly agile which proved useful in defensive play, however the motors turned out to be fragile and were prone to burning out, to counteract this we ran them at a lower voltage.
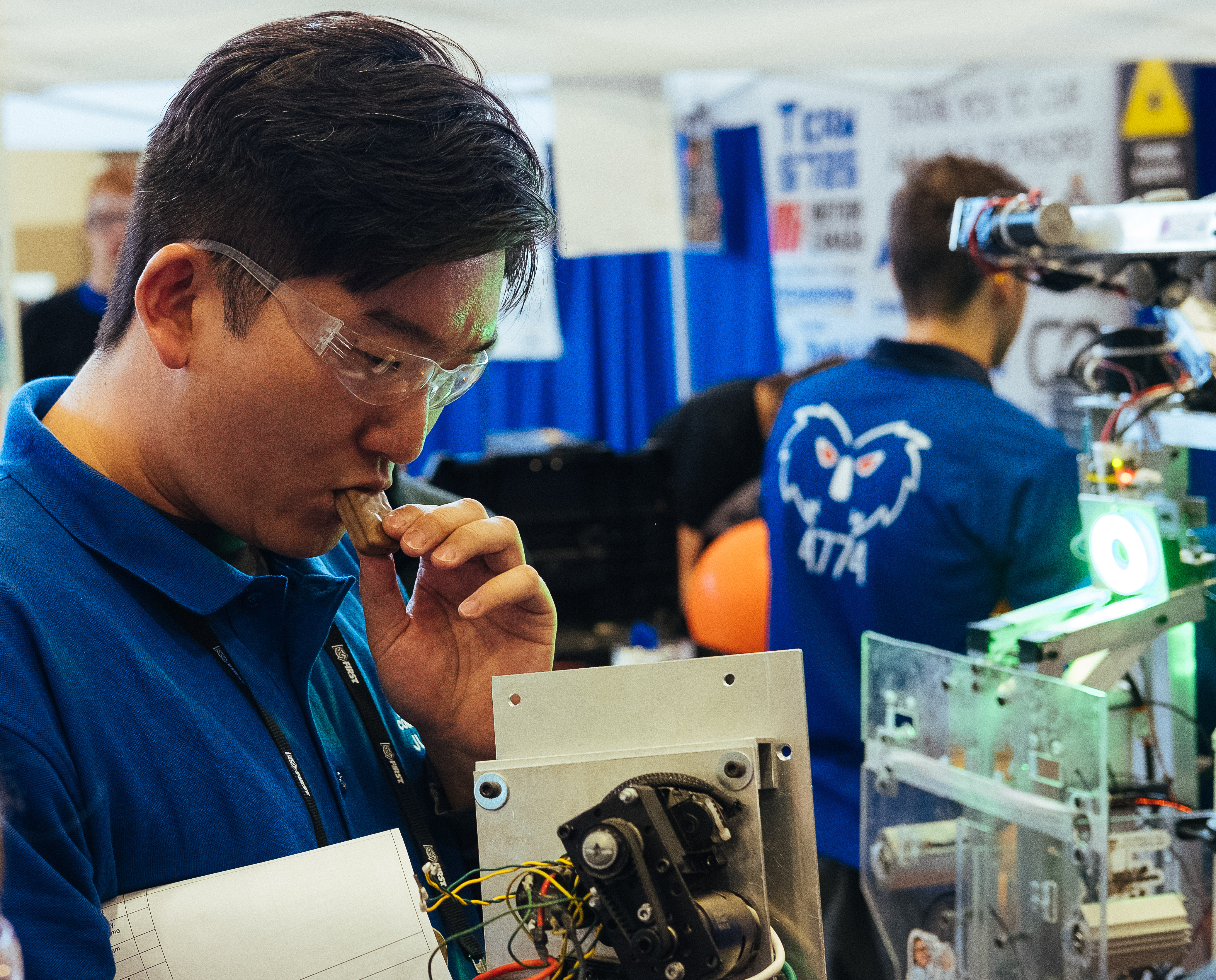