Design reviews, mechanism manufacturing, testing and improving robot code
After a very busy week of finalising the prototypes and starting to manufacture parts for the mechanisms the team is ready to test some of the final assemblies.
Intake
The final intake now has only 2 rows of wheels to capture and manipulate the cargo ball into the indexer.
The first row has compliant wheels in the centre to allow for compression and 2 omni wheels at the edges to assist in moving the ball to the centre of the intake.
The second row has smaller omni wheels and 2 rubber wheel in the center.
The first new componets of the intake are cut out on the CNC router.




Indexer
The indexer design was changed with the cargo ball transport from rubber belts to compliant wheels.
This results in a more reliable and predictable speed and control of the cargo ball.

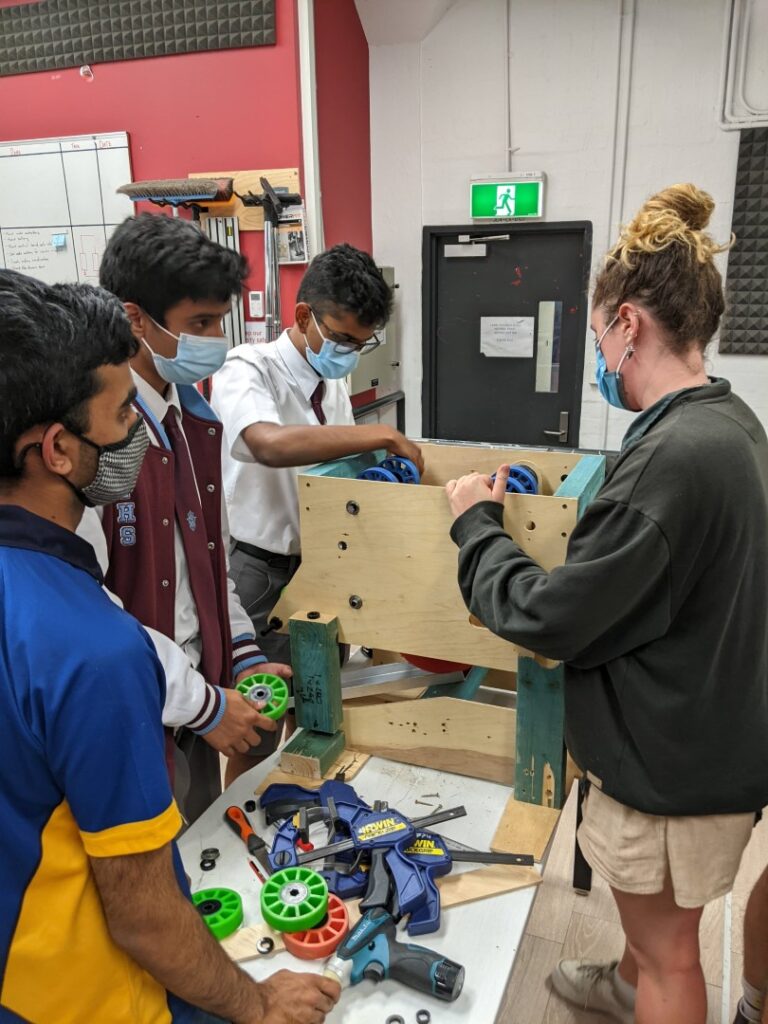

Shooter
The shooter and turret parts have been manufactured and assembled on the prototype indexer ready for testing.
The parts have been cut out on the team’s new CNC router that was proudly donated by Hullbot.



Drive Base
The prototype indexer, turret and shooter have been fitted to the drive base and connected to a temporary control system ready for testing.


Robot Code
New robot code was written by the software team to control the new swerve drive modules in autonomous mode.

