Final prototyping, testing, writing robot code and sponsor visit
David Bolt and Tom Wise, two directors of our Sponsor Warren Smith Consulting Engineers visited the teams workshop today for a tour, introduction to the team and to see the progress of the 2022 competition robot.
The final prototype mechanism were under test for cargo ball pick up and shooter accuracy.
Warren Smith Consulting Engineers have been supporting the team with sponsorship since 2015.
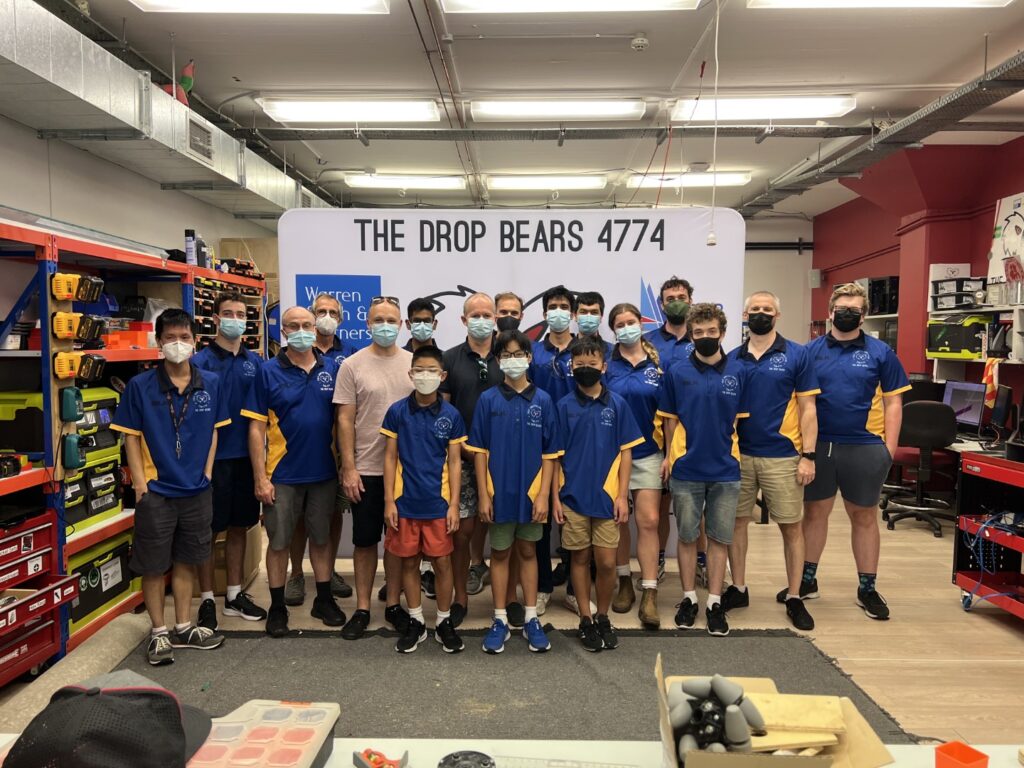
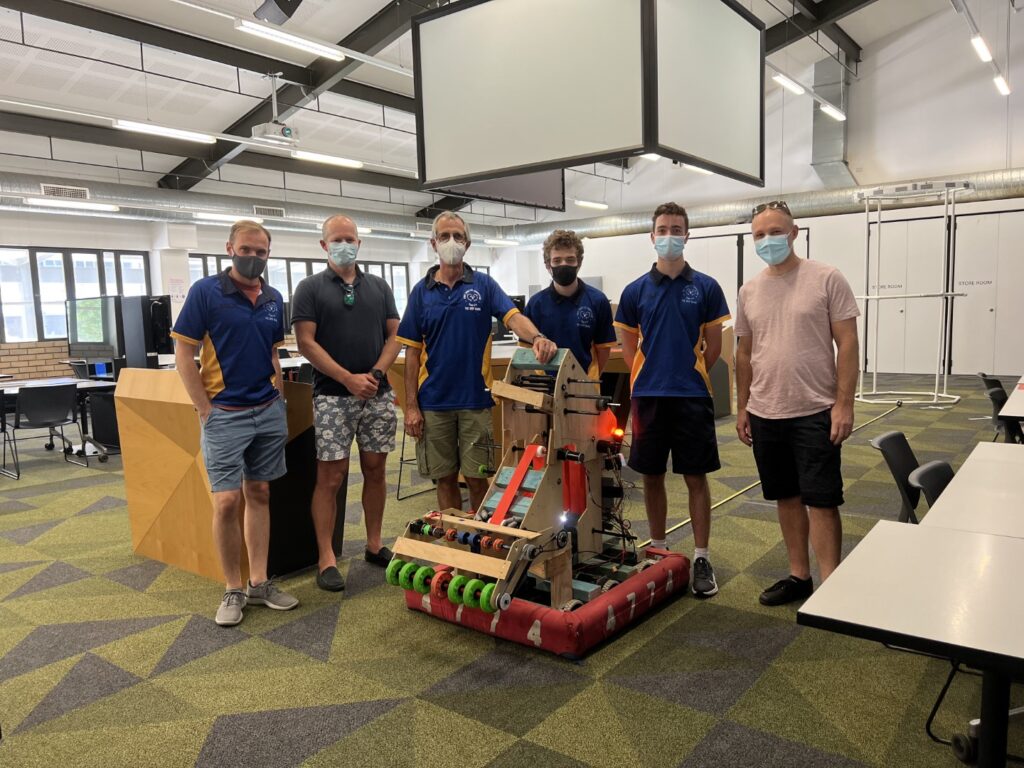
Intake
The final prototype of the intake now has 3 rows of wheels to capture and manipulate the cargo ball into the indexer.
The first row has compliant wheels to allow for compression, the second row has omni wheels to center the cargo ball and the third row with mecanum wheels as part of the indexer interface for final locating of the cargo ball under the transport belt.
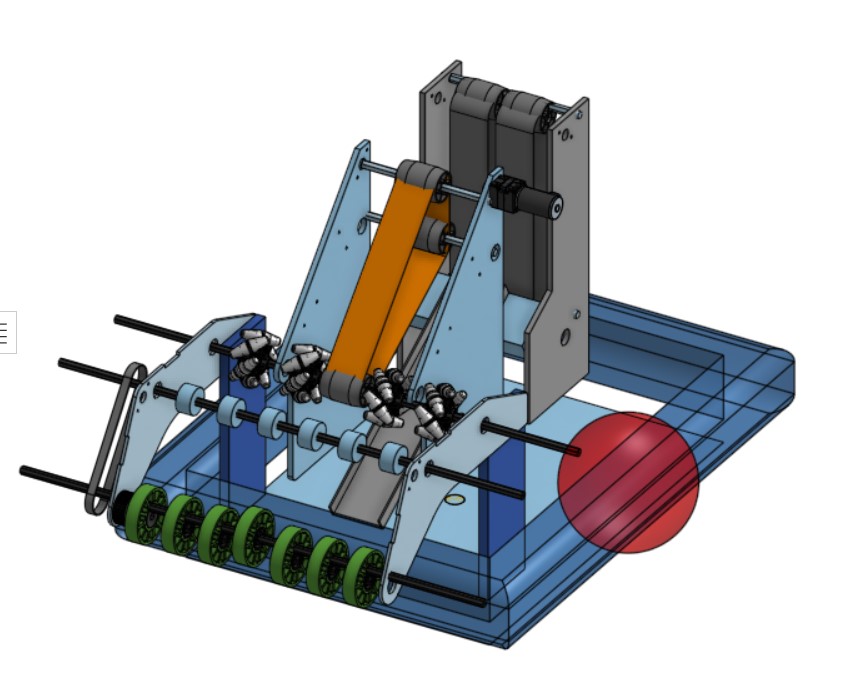
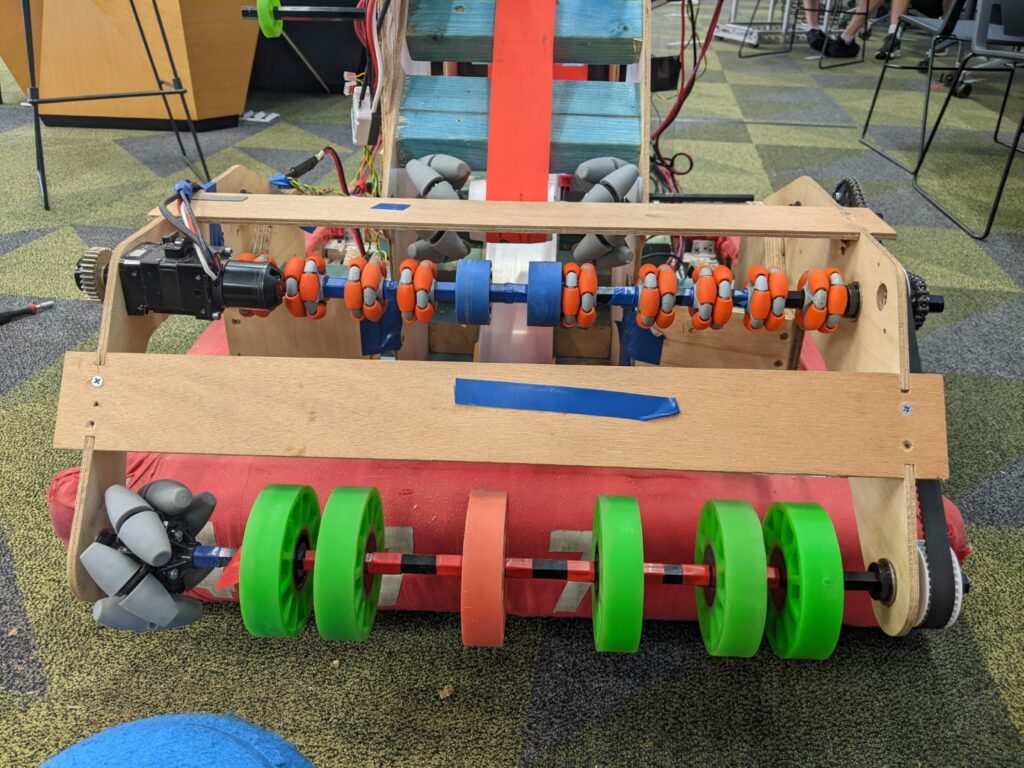
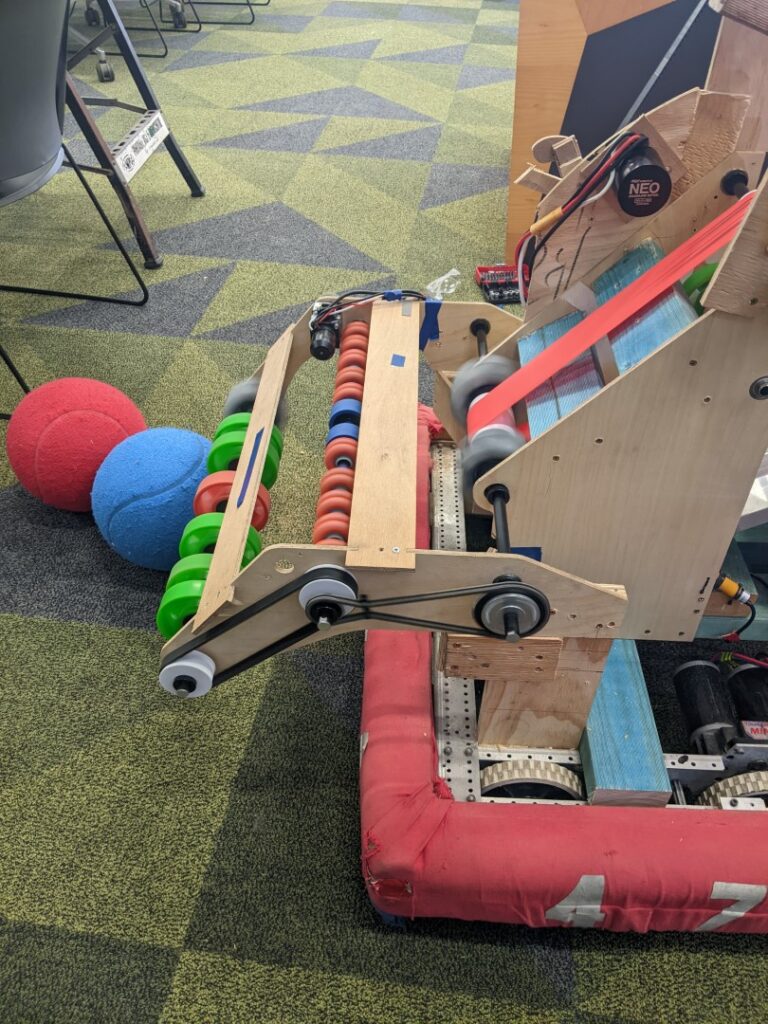
Indexer
The indexer stores and transports the cargo ball into the shooter.
A proximity sensor detects the presence of a cargo ball and stops the intake from picking up further cargo balls.
A colour sensor identified the colour of the ball and rejects it if an opposing alliance ball has been taken in. This prevents accidently scoring for the opposing alliance.
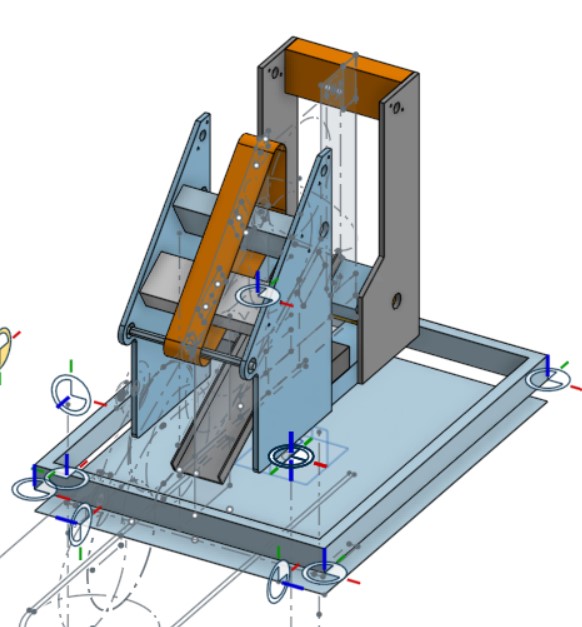
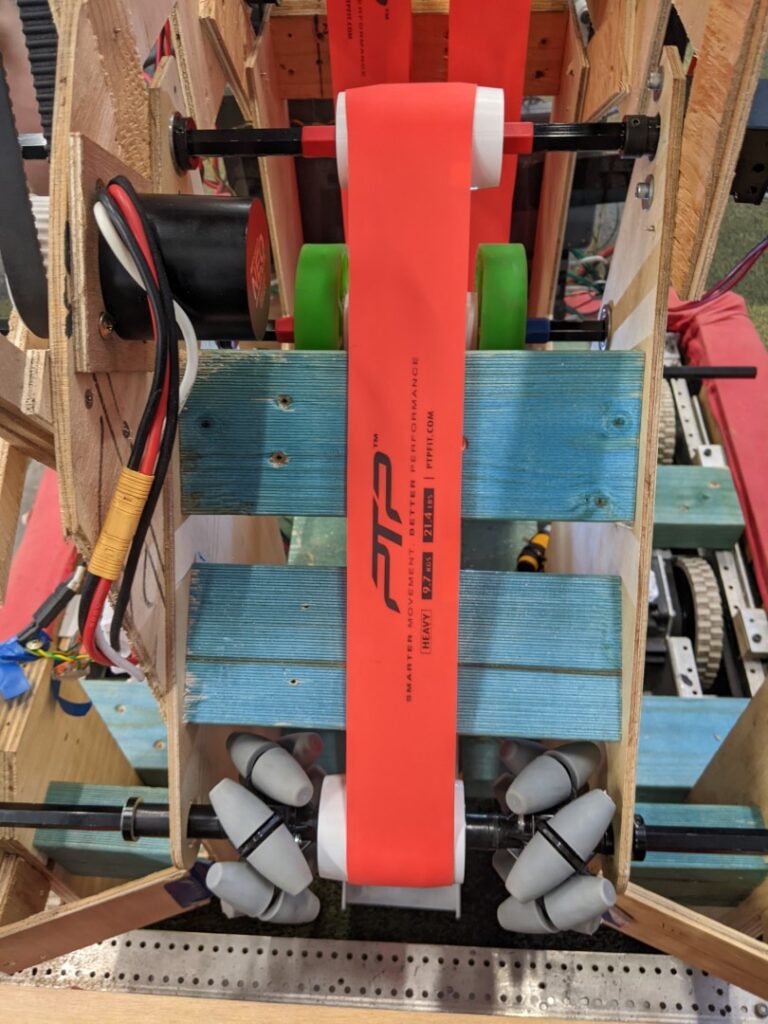
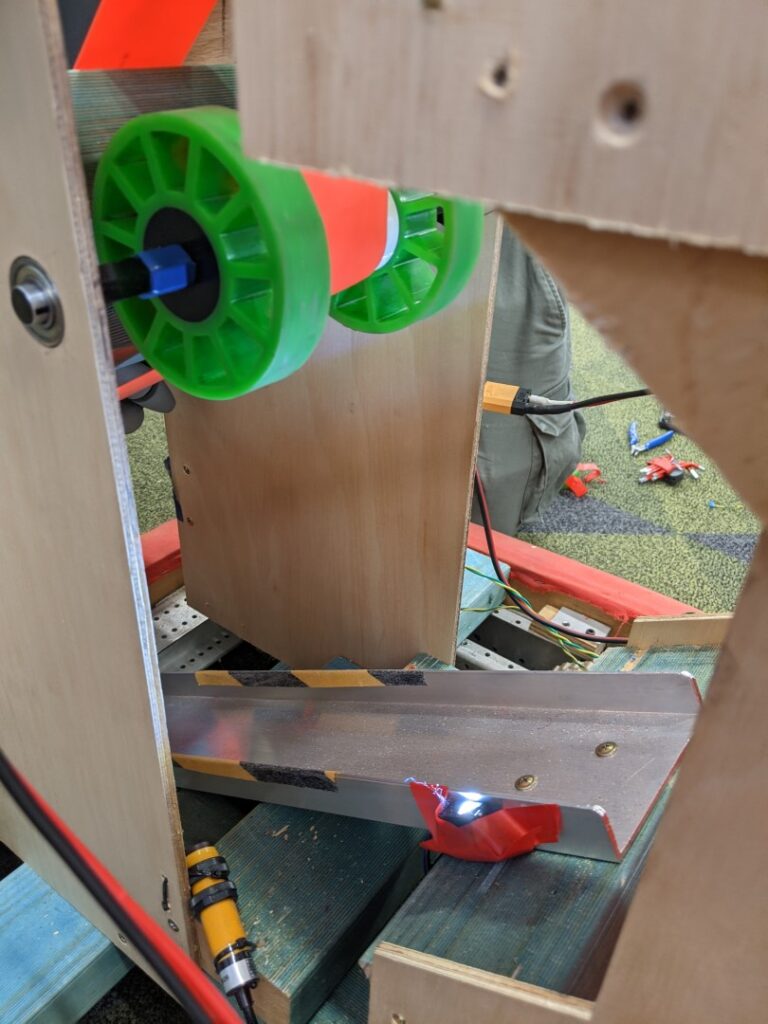
Shooter
The shooter prototype is used to test the effectiveness of the wheels and understand the relationship between wheel speed and the cargo ball trajectory.
A variable angle mount concept for the shooter was developed to understand the complexity.
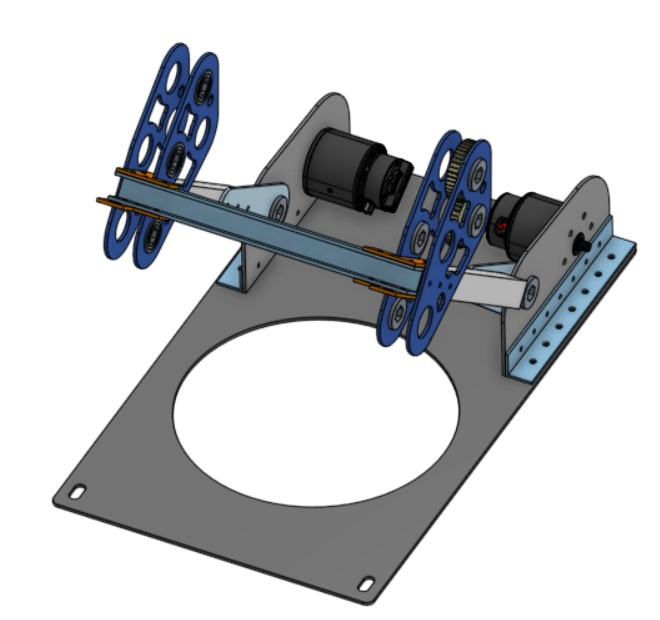
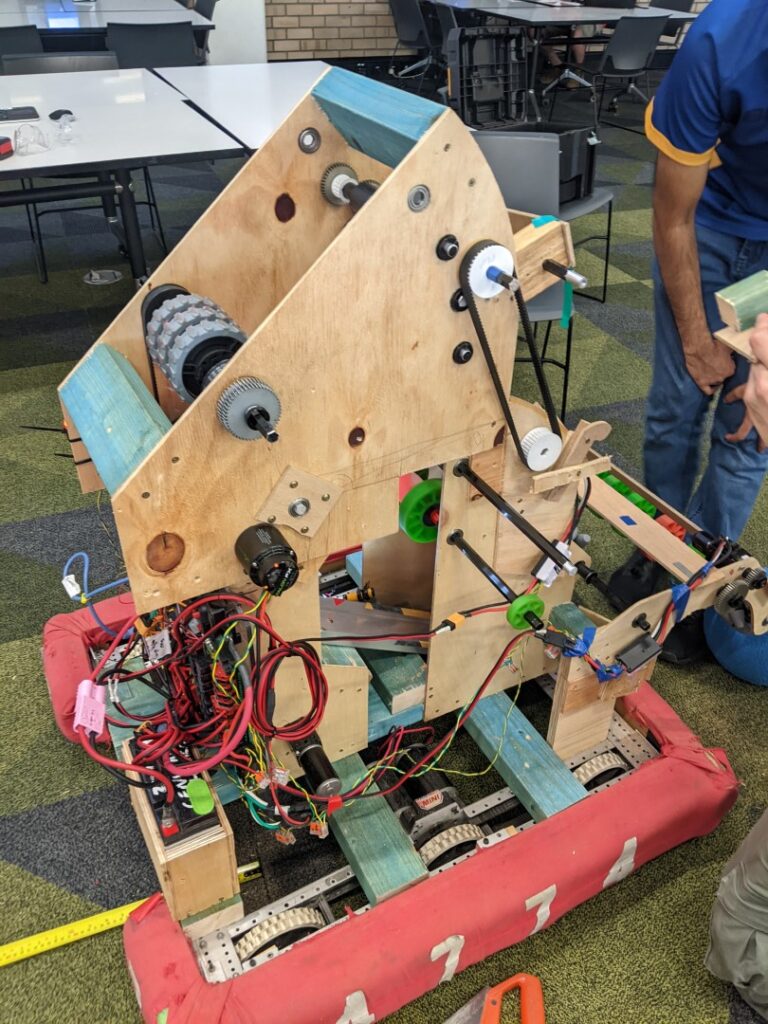
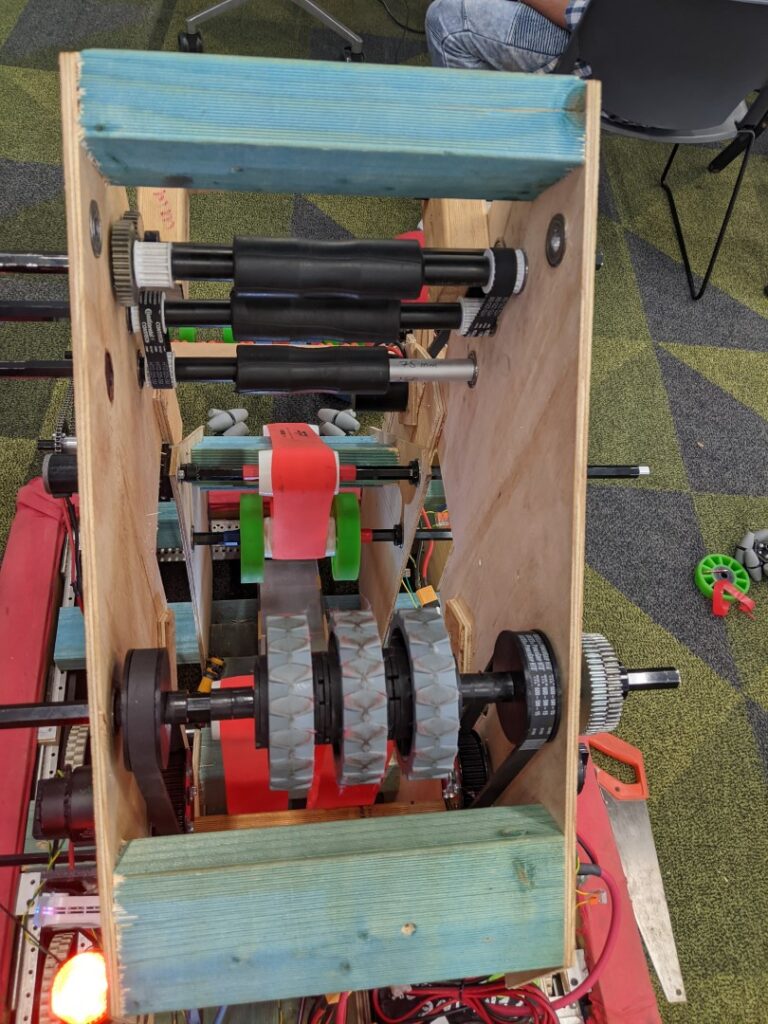
Drive Base
The team purchased 4 swerve drives MK4i from Swerve Drive Specialities and completed the drive base for testing.
A temporary robot control system was fitted and programmed to allow for initial driver training.
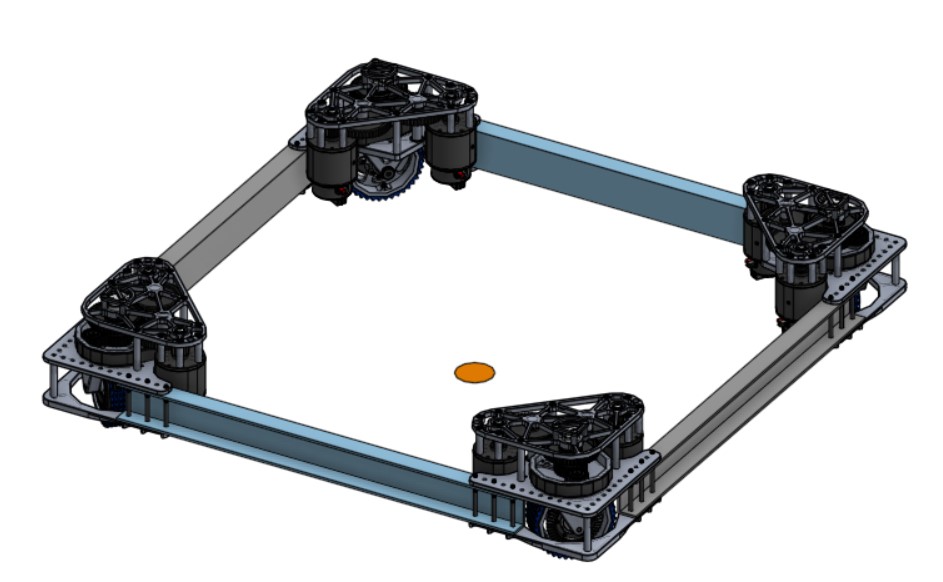
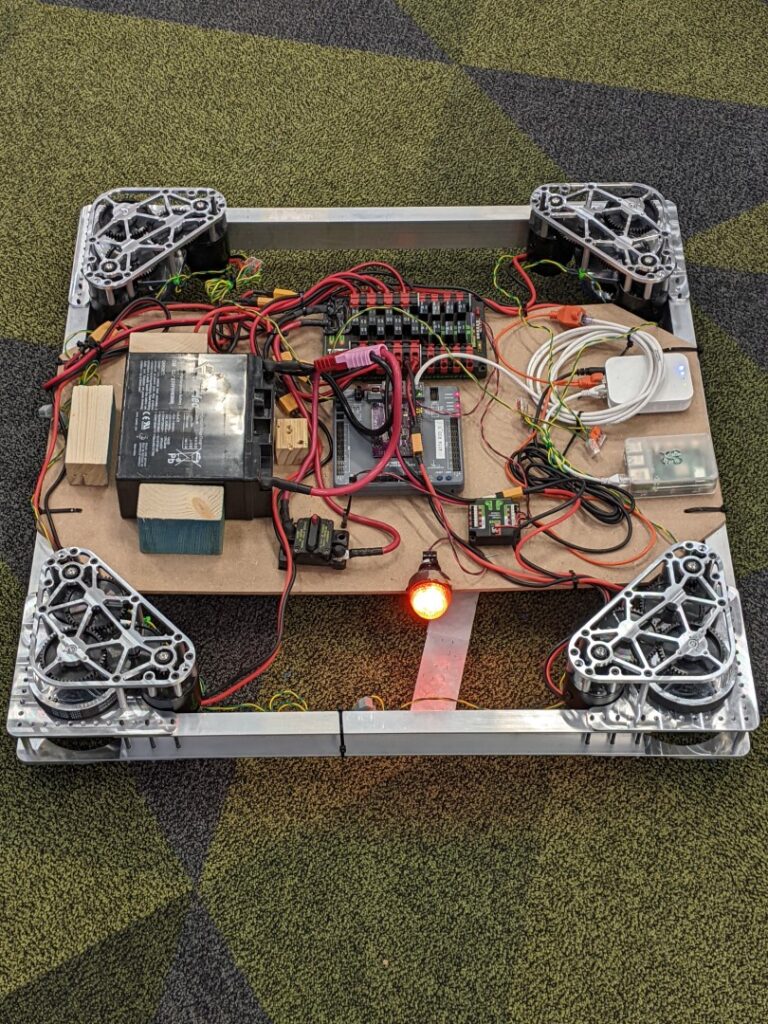
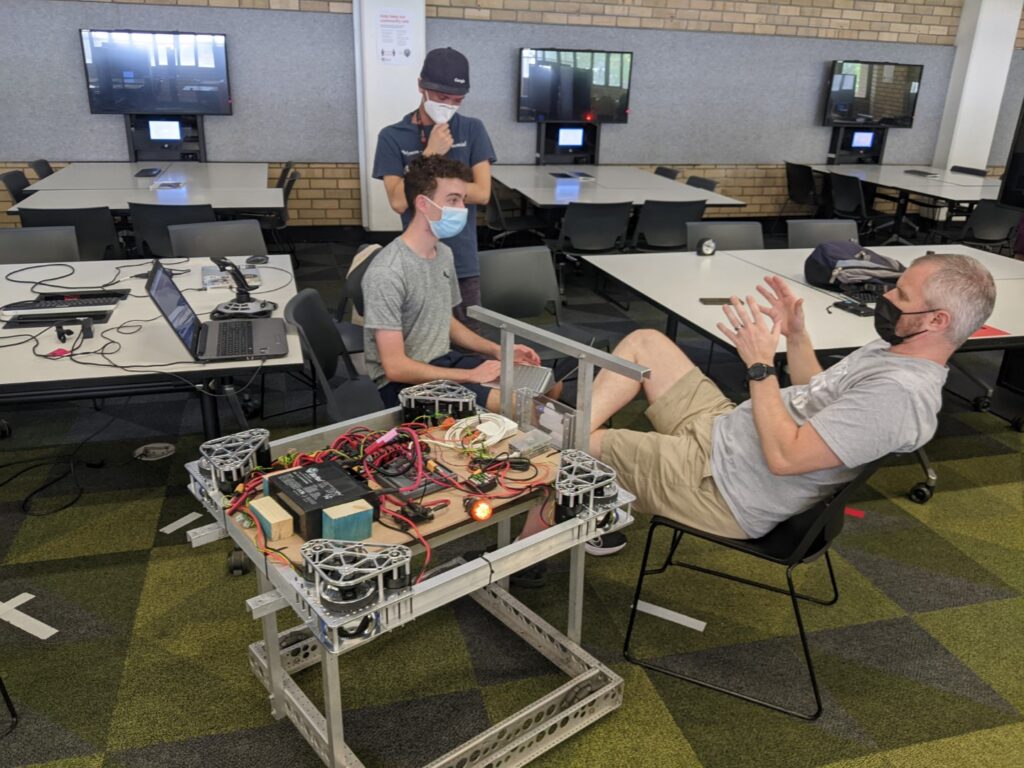
Robot Vision Code
Further testing and programming was done to improve the target location accuracy.
The image is filtered by green light reflected to identify the top of the hub and will be used to aim the shooter.
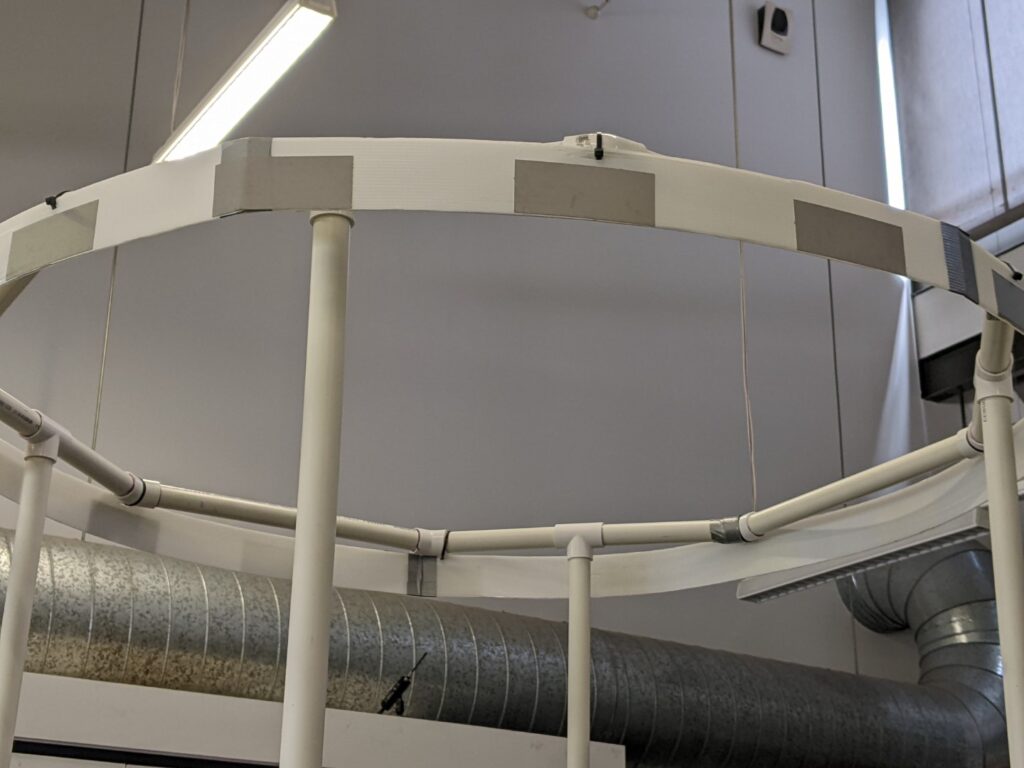
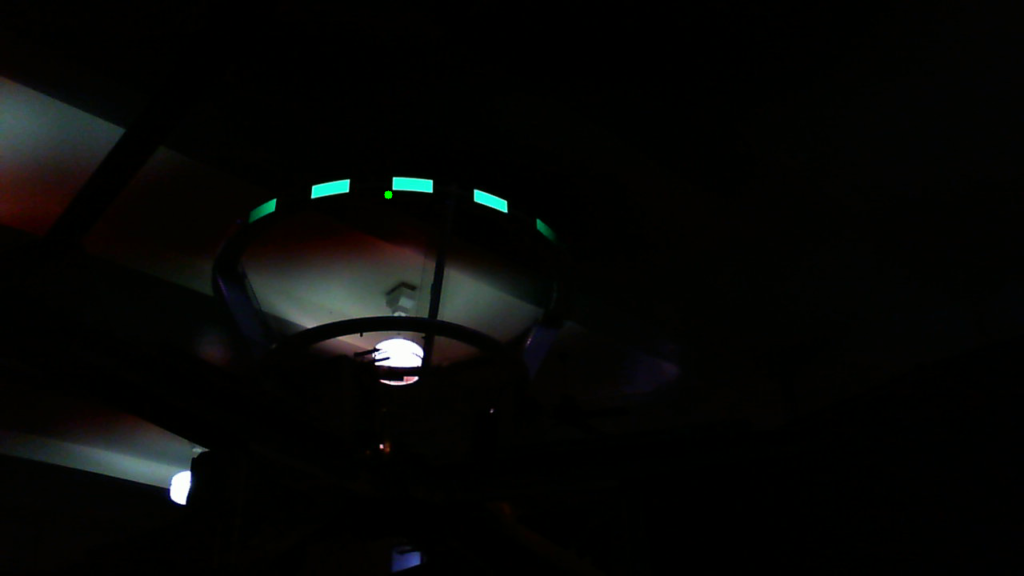
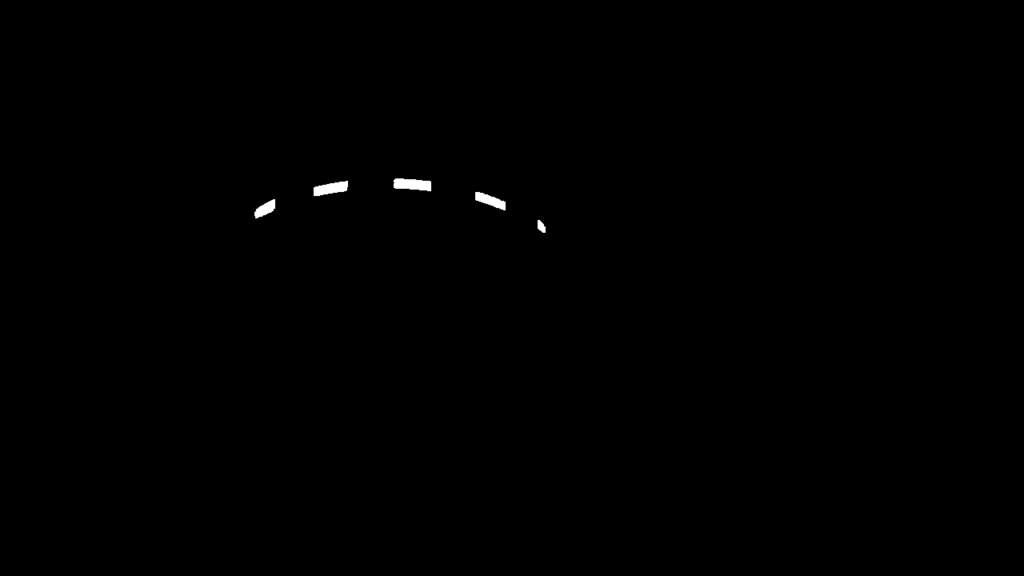